The maintenance requirements for their industrial air compressors are something that compressed air users should be aware of. The user can tell when a particular machine needs care when they are aware of its performance, operating characteristics, and service needs.
Underperforming air compressors can be expensive, dangerous, and inefficient. Fortunately, the majority of possible or impending faults exhibit early warning indications that are simple to identify for an experienced compressed air user.
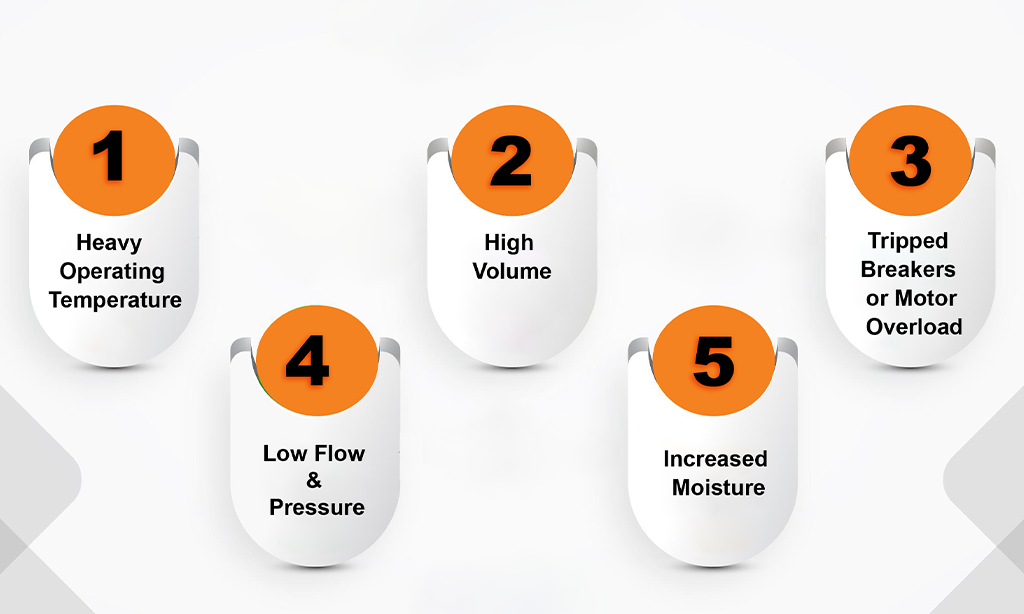
Heavy Operating Temperature:
All air compressors struggle with heat all the time. Huge amounts of heat are generated physically when air molecules are compressed, and the efficient dissipation of this heat is essential for the safe and dependable operation of compressors.
High Noise:
Although many compressor OEMs have been able to lower the total running noise of more recent models thanks to increasing technology, end users of compressed air should be aware of the noise that their compressors typically make under normal circumstances. Investigations should be done right away if there is a change in operation noise. Any bearing noise that cannot be explained, such as clicks, rattles, or rumbles, should always be immediately addressed because they may indicate a more serious issue.
Tripped Breakers or Motor Overload:
The majority of industrial air compressors have a safety shutdown feature that will turn them off automatically if the motor amperage goes over the permitted limit. When this defect causes a compressor to shut down, the root cause should be looked into right away. An authorized expert may be able to rapidly fix the problem in some cases with a small change.
Low Flow & Pressure:
A compressed air system that has been appropriately constructed should be able to fulfill the application’s requirements for airflow and pressure. The effects on a company’s bottom line might be disastrous if a compressed air system suddenly or mysteriously is unable to maintain proper pressure. The earnings of a corporation may suffer as a result of subpar product quality, facility outages, and decreased safety.
Increased Moisture:
Users of compressed air must just accept this inevitable result of the compression process. However, the quality, productivity, and dependability of a facility’s compressed air supply might be harmed by the presence of liquid water. Because of this, the majority of end users use air treatment tools like dryers, filters, and mist eliminators to get condensation out of their air systems
Conclusion:
Your air compressor will likely go through the typical wear and tear of an industrial setting. To know more kindly contact us at Milestone Pneumatics or email at ccs@milestonepneumatics.com